Verification Report - Surrey
What is it?
This is a document that will include all the information required to demonstrate that the site has been cleaned up in accordance with the appropriate legislation and as specified in the Remediation Strategy. This report is to demonstrate that the site is suitable for the proposed use.
The contents will be set out in the Verification Plan contained within the Remediation Strategy. We will also prepare a Verification Checklist for you so that you know exactly what it is you need to record and keep for inclusion the Verification Report.
It must be remembered that the report is not confirming the site is "uncontaminated" rather that it is suitable for the proposed use. If you are purchasing a site with a verification report stating the site is suitable for use as an office further investigation is likely to be required if the new proposal is for residential use.
When should it be prepared?
The short answer is as soon as possible. The problem often arises because remediation generally includes placing of clean sub and topsoil to external areas, one of the last operations and submission and approval of a Verification Report will often be a pre-occupation planning condition. It is never too early to call us to discuss how we are going to manage verification to ensure approval is gained as swiftly as possible.
Verification Checklist
We will issue a Verification Checklist when we prepare your remediation strategy so that the necessary records can be obtained throughout the project. The requirements will vary from project to project but may include:
Imported Fill Material
- Certification from supplier confirming compliance with the remediation strategy
- Volume imported, with supporting purchase records or other documentation
- Transportation documentation
Waste Disposal
- Waste transfer tickets from transporter and receiving facility, example attached
- Volume disposed off-site
Gas Protection Measures
- Full "as-built" drawings and specifications
- Quality control documentation
- Photographs of installation
- Independent verification of membrane installation
Surface Water Management
- Design specifications and drawings
Drinking Water
- Confirmation from water supplier of installation of barrier pipe, e.g. receipt
- Photographs of pipe in trench
- Record of any site visits by water supplier to inspect barrier pipe installation
External Hardstanding
- Cross-section drawings showing 300mm construction thickness
Remedial Ground Works:
- Before and after photographs showing removal of impacted soil from areas to be remediated, with a measuring staff or other means of establishing scale, example attached
- Original and Final survey levels, and levels following site strip
- Confirmation that no unforeseen visual or olfactory evidence of contamination was encountered during the works.
Who needs a copy?
The local authority and the Environment Agency will want to see the report if they have required the work to be undertaken. When the land is sold the prospective purchaser will need to see the report to be assured that the land is suitable for the existing or proposed use.
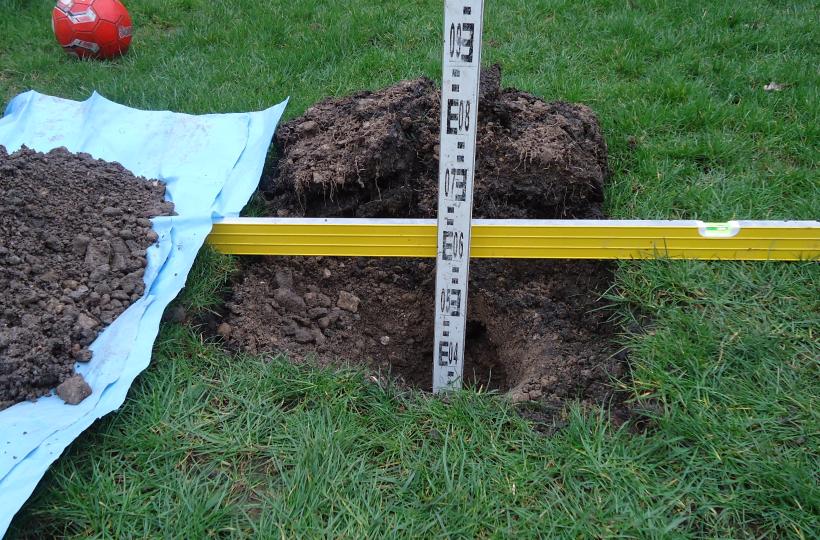
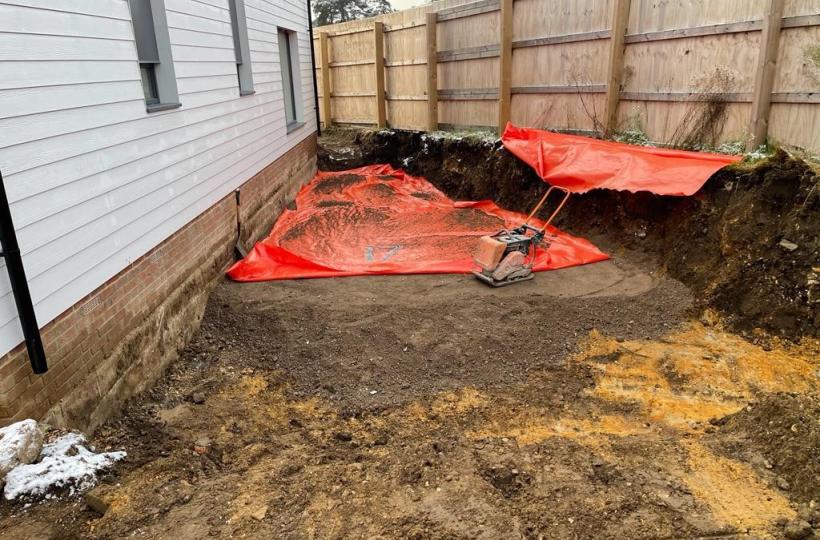
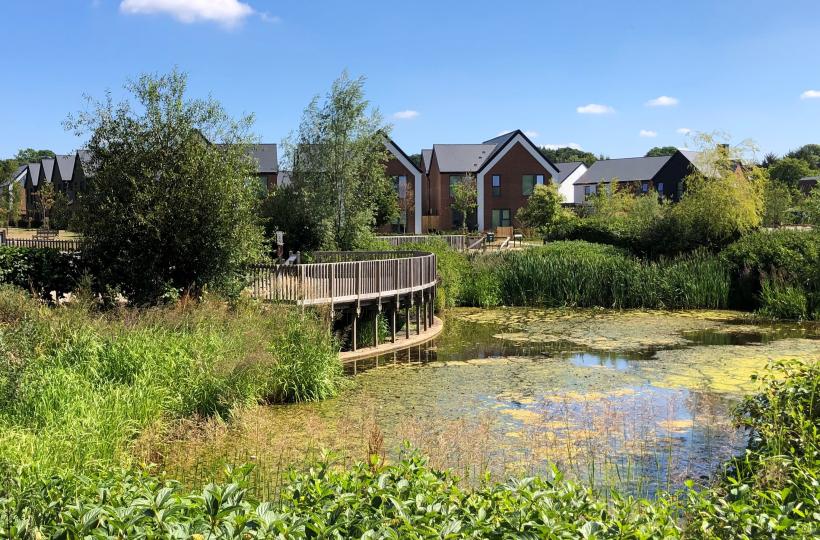
View of completed project from communal amenity area. No-dig layer and hi-viz membrane being laid ready for sub-soil and topsoil.
The site forms part of the wider Princess Royal Barracks, Deepcut which was constructed in 1913. Prior
to this, the wider site was heathland.
The development comprises twenty-one properties, some terraced, others detached, with three, four and five bedrooms.
A remediation strategy had been prepared and specified:
The following works are considered necessary during the Enablement Phase of works:
• Task 1: Hand-picking and disposal of all visible ACM at surface level.
• Task 2: Breakout hardstanding, excavate sub-base and stockpile arisings accordingly.
• Task 3: Excavate and remove existing concrete drainage pipe from ‘Access Way’.
• Task 4: Delineate and remove known asbestos soils with >0.001% w/w asbestos and visible ACM.
• Task 5: Stockpiling and disposal of unsuitable material off-site to an appropriate registered waste
facility.
• Task 6: Excavate ‘buffer zone’ to pub plot.
• Task 7: Confirmation of Cover System Requirements
The following tasks apply to all of the above:
• Task 8: Asbestos in soils (general advice)
• Task 9: Hand-pick of asbestos containing materials, where encountered.
• Task 10: Record, delineate and remove any significant visible asbestos contamination.
• Task 11: Off-site disposal of unsuitable of waste material.
• Validation during enablement works.
The following works are considered necessary during the Construction Phase of works:
• Task 12: Installation of clean service corridors.
• Task 13: Over-Excavation of Service Trenches and Backfilling with ‘Clean’ Soil
• Task 14: Installation of the Engineered Cover System.
• Task 15: Installation of ground gas protection measures in line with CS2.
• Validation during construction works.
Four cover systems were specified for different areas of the site:
1m Engineered Cover System comprising: 200mm No Dig Layer, Geotextile Membrane, 800mm Subsoil and Topsoil (min 150mm Topsoil)
600mm Engineered Cover System comprising: 150mm No Dig Layer, Geotextile Membrane, 450mm Subsoil and Topsoil (min 150mm Topsoil)
450mm Engineered Cover System comprising: Geotextile Membrane, 450mm Subsoil and Topsoil (min 150mm Topsoil)
Simple cover system comprising: 150mm Topsoil, subsoil to make to formation level
GO CLS were commissioned to monitor the remedial works and prepare verification reports. Excavation depths were recorded and sub-grade sampled and tested to ensure contaminated material had been removed. Imported soils were sampled and tested and depth of layers monitored to ensure compliance. Verification reports were prepared phase by phase as the project progressed.